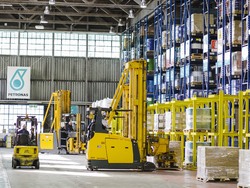
La visita all’impianto di Villastellone e all’adiacente centro R&T di Santena è stato un vero e proprio viaggio nel cuore produttivo di Petronas, un viaggio che ci ha permesso anche di scoprire la sua autentica anima innovativa.
Tutto questo è stato il viaggio in PETRONAS: una giornata nel cuore produttivo e nell’anima tecnologica di una società multinazionale, classificata come una delle più grandi aziende a livello mondiale.
PLI: 100 anni di storia ed esperienza
Petronas Lubricants International (PLI) è la divisione globale di Petronas che si dedica alla produzione e commercializzazione di lubrificanti.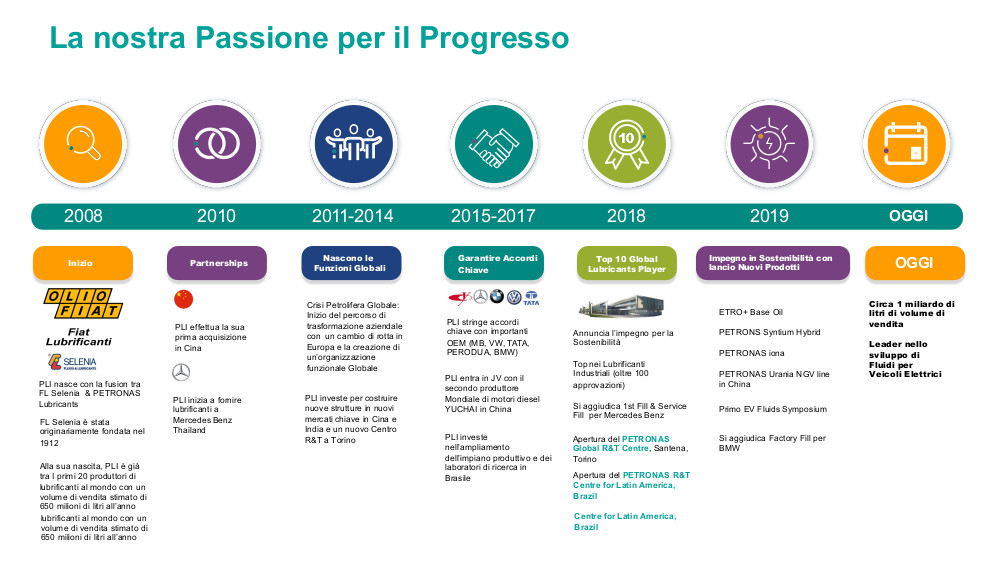
Sin dalla sua fondazione nel 2008, PLI è diventata l’azienda di lubrificanti in più rapida crescita al mondo, un partner da sempre focalizzato sulla ricerca delle migliori soluzioni nel campo dei lubrificanti e dei fluidi.
Forte di oltre un miliardo di litri di lubrificanti venduti ogni anno, PLI è oggi uno dei principali player nello sviluppo di fluidi per veicoli elettrici, dando un forte contributo allo sviluppo di una mobilità green per un futuro sostenibile.
Il Global R&T Center: un polo d’eccellenza
Con sede a Kuala Lumpur (Malesia) e stabilimenti in ogni continente, PLI ha una presenza globale. Ma è in Italia che la multinazionale ha voluto fortemente investire, inaugurando nel 2018 il Global Research & Technology Centre di Santena (TO), un centro di eccellenza per la progettazione e lo sviluppo di prodotti in partnership, realizzati su misura e rispondenti alle specifiche esigenze dei costruttori.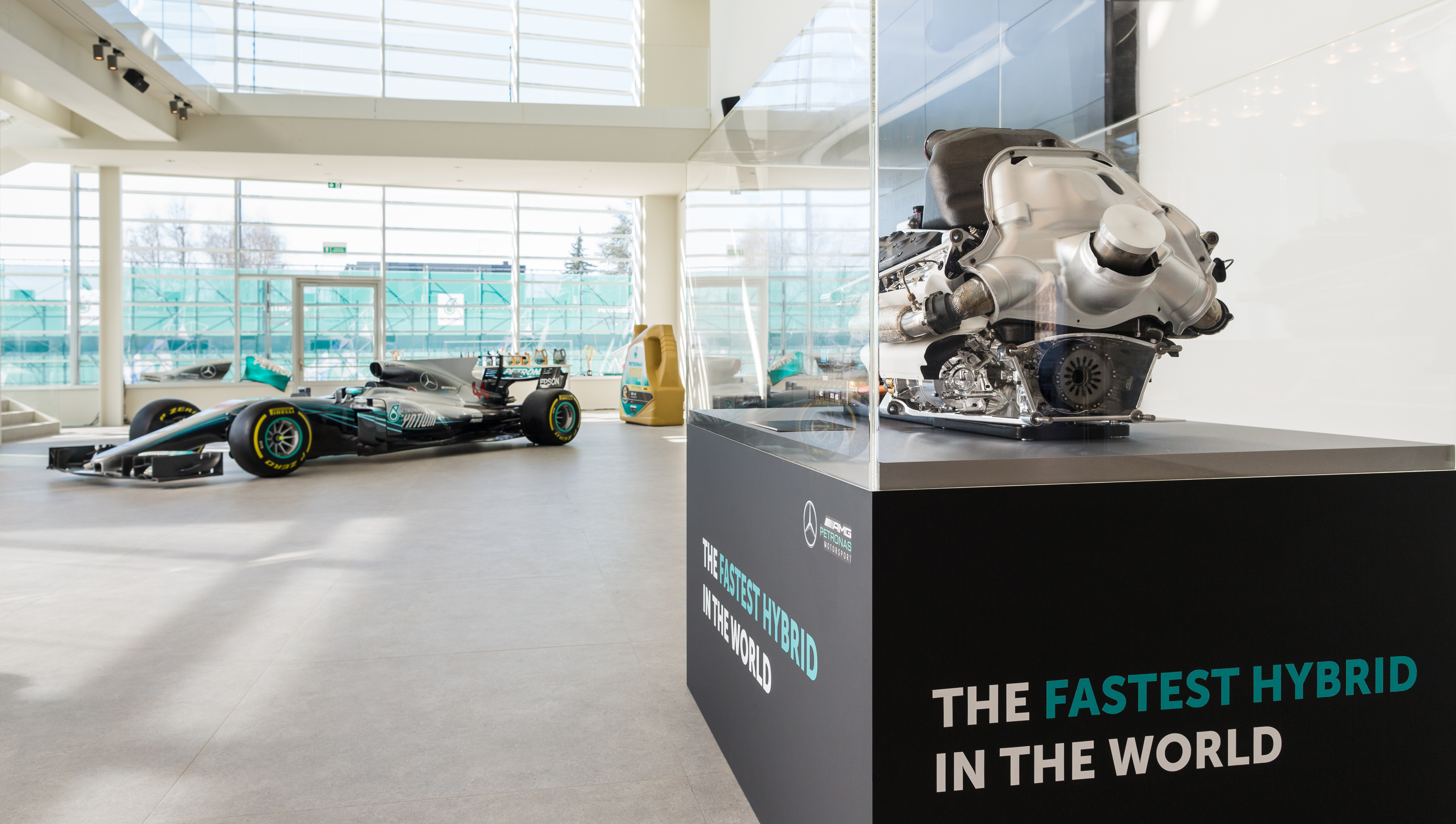
Il centro è anche un esempio di sostenibilità, sia in ambito Ricerca e Tecnologia, sia da trasferire lungo tutta la supply chain.
Dal 2018, infatti, PLI ha indirizzato il 75% dei suoi investimenti in ricerca e tecnologia (R&T) verso prodotti in grado di ridurre le emissioni dei veicoli e prolungarne la durata, sostenendo l’obiettivo più ampio di un veicolo a zero emissioni entro il 2050.
Il Petronas Global Research & Technology Centre è inoltre impegnato costantemente nella ricerca sui fluidi per la mobilità elettrica. I motori EV funzionano in modo diverso da quelli tradizionali: per questo, i ricercatori del centro studiano come ottimizzarne le prestazioni, anche grazie alla collaborazione diretta con i costruttori di veicoli.
Da questo impegno, è nata la gamma di fluidi Petronas Iona, specifica per i veicoli elettrici, che accompagna gli automobilisti nel loro viaggio verso un futuro più sostenibile.
Di recente, inoltre, il centro R&T di Santena è diventato un Energy Provider: i banchi meccanici sono stati riprogettati per recuperare l'energia prodotta durante i test di collaudo, invece di dissiparla come calore sprecato. Questa energia viene poi rimessa in circolo per alimentare il resto del centro, mentre l'eventuale surplus viene immesso nella rete elettrica e inviato a un fornitore locale di elettricità, a vantaggio del territorio e della comunità locale.
I laboratori
Varcate le porte del centro, si entra subito nell’area riservata ai camici bianchi. Dietro le vetrate, si susseguono tre laboratori. Il primo è quello di chimica analitica, dotato di apparecchiature da cromatografia, da spettroscopia e altre analisi di tipo elementare; è qui che si analizzano le sostanze per verificare se possono essere impiegate nella formulazione di una nuova ricetta.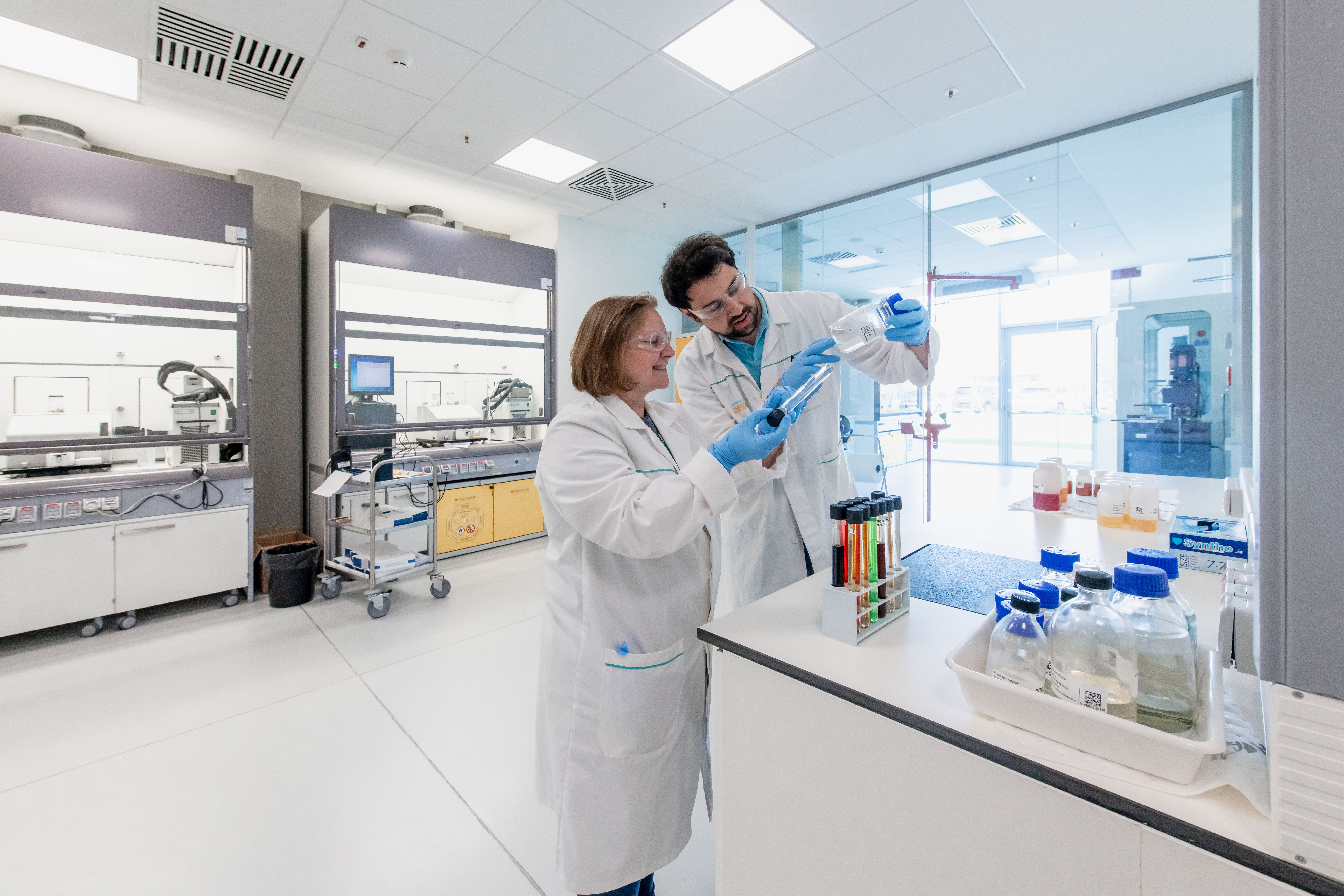
Il secondo laboratorio contiene apparecchiature per analisi chimico-fisiche volte a valutare caratteristiche come viscosità cinematica e dinamica, punto di infiammabilità, acidità e basicità, conducibilità elettrica, calore specifico, resistenza alla corrosione ed ossidazione come capacità protettiva dell’olio.
Qui si trova lo SpectrOil, un apparecchio basato sulla spettroscopia ad emissione atomica, che serve per determinare i metalli di usura presenti nell’olio esausto. Questo strumento ha due gemelli: uno in Mercedes e uno sui circuiti F1.
Il fatto che i dati dei tre strumenti siano confrontabili dimostra che la ricerca gode simultaneamente dei dati raccolti dalle tre differenti esperienze e che i ricercatori PLI lavorano in sinergia con gli OEM.
Il terzo laboratorio è quello di tribologia, ovvero la scienza che studia gli attriti e la compatibilità tra materiali. In questo laboratorio si effettuano a livello micro i test che si faranno poi nei mechanical test a livello macro.
Sale prove motore e workshop
Dai laboratori si accede poi alle sale prove motore, dove si effettuano i test sui motori o sulle componenti meccaniche dei veicoli quali assali, cambio e trasmissioni.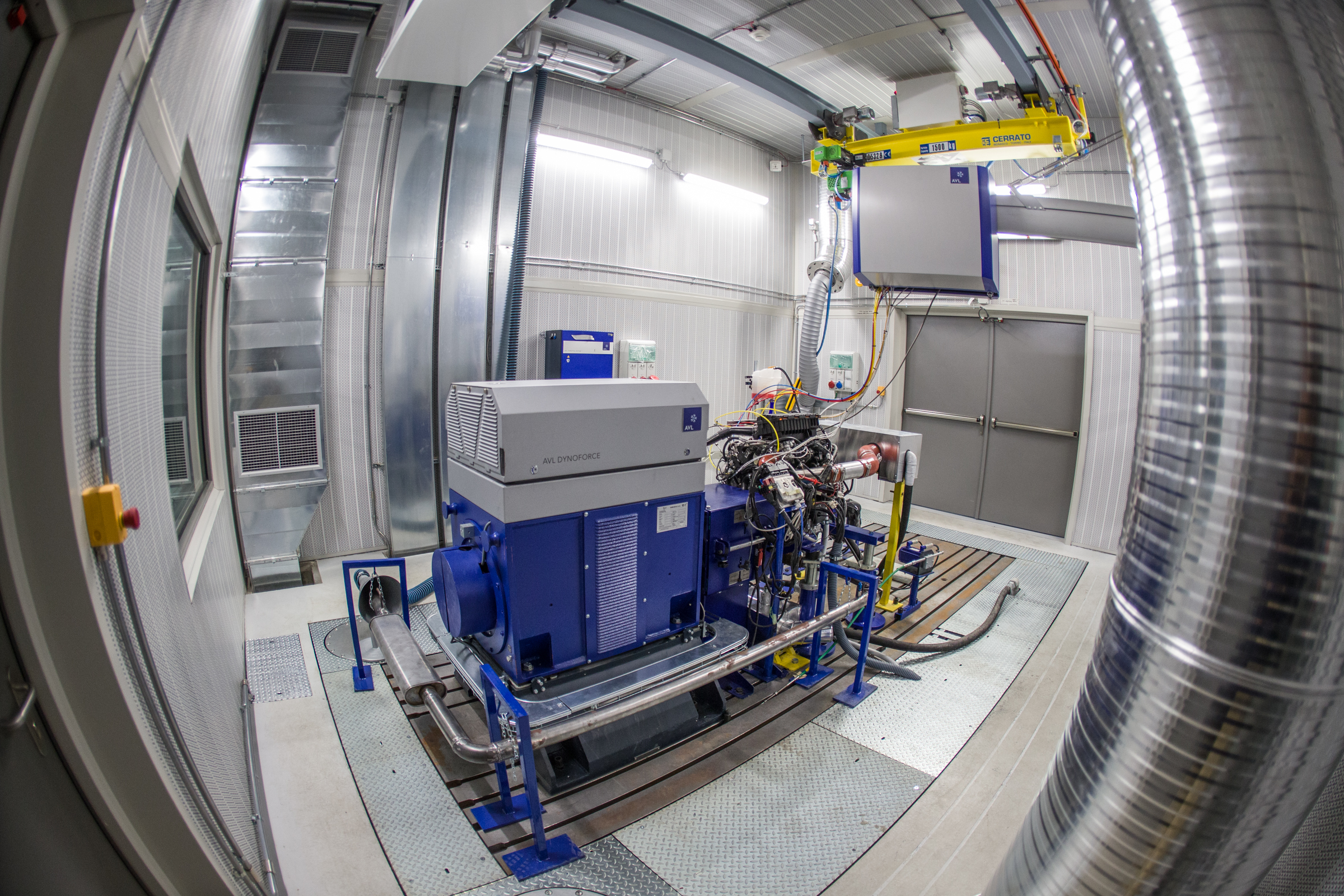
Al momento ci sono sei sale prova, di cui quattro statiche e due dinamiche; da segnalare, che ognuna delle sale si può allestire a seconda della necessità.
Nell’area workshop si prepara il motore per i test e per il banco rulli.
È qui, che una volta terminati i testi, il motore viene smontato per valutare l’usura delle sue componenti (sui primi banconi entrando di solito si vedono componenti di motori smontate per la valutazione dello stato di usura, mentre dopo la seconda fila di banconi si trovano spesso motori in preparazione per le prove di fuel economy sul banco rulli).
L’impianto produttivo: una storia di fluidi
Solo una striscia di terreno separa il moderno complesso di ricerca e sviluppo di Santena dallo storico impianto produttivo di Villastellone. Quest’ultimo è un impianto che trasuda fluidi e innovazione, perché è qui che si sono alternate aziende come Olio Fiat prima e Fiat Lubrificanti poi, passando per FL Selenia fino a Petronas Lubricants.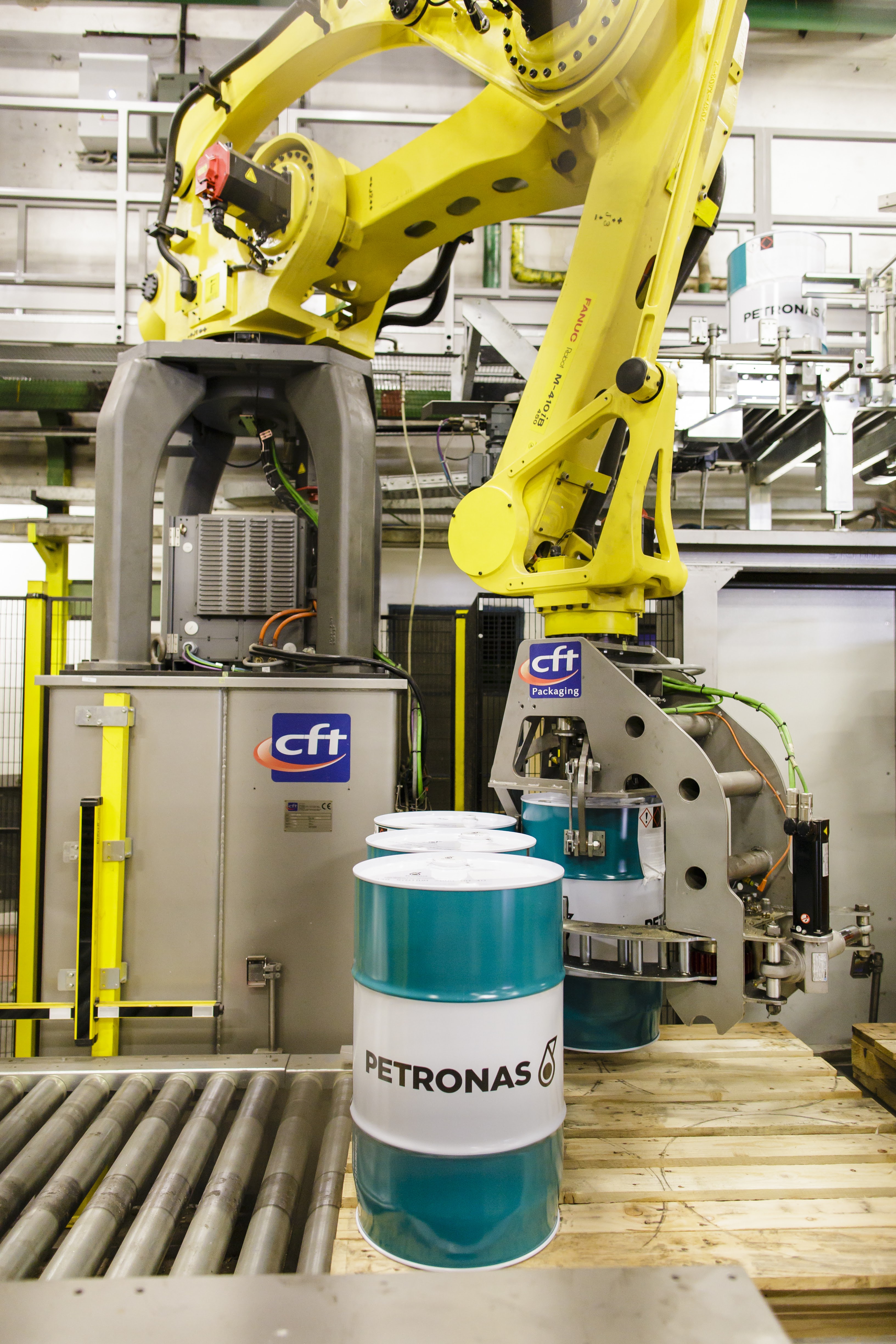
Il nostro tour parte dal parco serbatoi, in parte visibile, perché in superficie, in parte invece interrrato. Qui si trovano i serbatoi che alimentano la blending tower con le materie prime necessarie, e i serbatoi in cui vengono stoccati alcuni prodotti prima di venire confezionati o venduti sfusi trasportati in autobotte (ad esempio gli oli venduti agli impianti di primo riempimento).
Per quanto riguarda le materie prime stoccate, si tratta nella maggior parte dei casi di oli base che vengo portate ai miscelatori mediante pompe. In ottica di sostenibilità, serbatoi e pompe sono dedicati a specifiche famiglie di prodotto, in modo da limitare i lavaggi quando si inserisce un prodotto nuovo nel serbatoio o si usa la pompa per alimentare un blender.
Gli additivi, invece, sono spesso stoccati in fusti.
La torre di miscelazione
La “Blending Tower” è composta da 11 miscelatori (due automatici e nove manuali) che lavorano con una programmazione su base settimanale e un ordine di produzione giornaliero.I miscelatori sono divisi per famiglia di semilavorato (6 per oli motore, 2 per trasmissioni, 2 per industriali e 1 dedicato alle piccole produzioni e ai F1). La destinazione d’uso specifica è necessaria al fine di evitare fenomeni di contaminazione fra semilavorati con caratteristiche molto diverse ed evitare sprechi di materia prima per la pulizia del sistema.
La miscelazione avviene intorno ai 45°-50°C in leggero vuoto per permettere all’acqua di evaporare; a seconda all’applicazione a cui è destinata, una ricetta può contenere dal 95 al 75% di olio base e dal 5 al 25% di additivi.
Il confezionamento
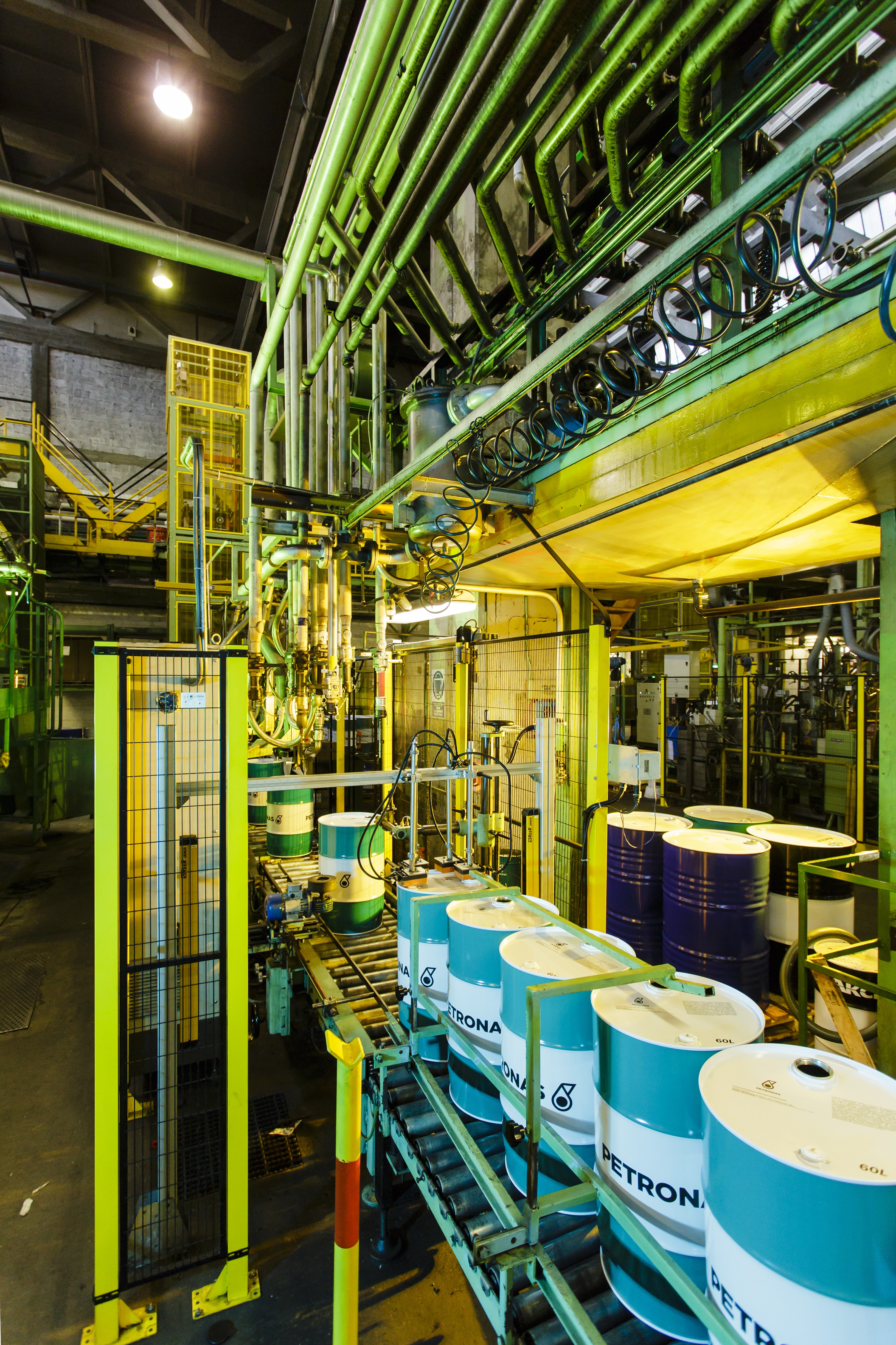
Taniche in plastica da 1 e 2 litri, taniche in metallo, taniconi da 20 litri e fusti: sono i diversi formati, a cui corrispondono linee di riempimento diverse.
Tutti gli imballi arrivano dal magazzino imballi vuoti per via aerea, direttamente alle linee di riempimento.
Il semilavorato invece viene portato alle linee tramite il manifold, una matrice di pompe che dai blender o più spesso dai serbatoi di stoccaggio porta il semilavorato alle linee.
Per la pulizia delle tubature si utilizza il pig e avvinamenti successivi (il pig è una palla con delle lamelle metalliche che raschia via dalle pareti il prodotto che vi era passato in precedenza); questo metodo consente di risparmiare 90 tonnellate di prodotti all’anno, che diversamente diverrebbero prodotto di scarto.
Ogni linea riempie, etichetta, inscatola e applica il numero di lotto ai prodotti, per cui da ogni linea esce il prodotto così come viene stoccato, pronto per andare ai pallettizzatori.
Tutti gli imballi arrivano dal magazzino imballi vuoti per via aerea, direttamente alle linee di riempimento.
Il semilavorato invece viene portato alle linee tramite il manifold, una matrice di pompe che dai blender o più spesso dai serbatoi di stoccaggio porta il semilavorato alle linee.
Per la pulizia delle tubature si utilizza il pig e avvinamenti successivi (il pig è una palla con delle lamelle metalliche che raschia via dalle pareti il prodotto che vi era passato in precedenza); questo metodo consente di risparmiare 90 tonnellate di prodotti all’anno, che diversamente diverrebbero prodotto di scarto.
Ogni linea riempie, etichetta, inscatola e applica il numero di lotto ai prodotti, per cui da ogni linea esce il prodotto così come viene stoccato, pronto per andare ai pallettizzatori.
Pallettizzazione e magazzino prodotti finiti
Divisa in linee per scatole (piccoli formati) e fusti e taniconi (grandi formati), qui i prodotti vengono pallettizzati in modo totalmente automatico, filmati e arrivano al magazzino attraverso un nastro trasportatore. Nel magazzino a ogni pallet viene applicata un’etichetta generata dal gestionale della logistica, che assegna un posto nello scaffali.Logistica
Una volta che la logistica riceve un ordine di spedizione, produce la bolla e fa preparare il carico nella baia, il gestionale del magazzino dice agli operatori quali pallet di prodotti prendere in base alla data di confezionamento, in modo da non tenere mai in magazzino i prodotti troppo a lungo. Il carico viene disposto nella baia secondo i criteri di distribuzione del peso necessari per il trasporto, successivamente all’arrivo del camion questo viene caricato.
Sostenibiità anche nel pack
Anche il packaging dei prodotti Petronas Syntium è stato sviluppato per essere più sostenibile: le nuove taniche Petronas Ecovent da 20 litri contengono fino al 50% di plastica riciclata Post Consumer Resin (PCR) e, grazie al sistema brevettato anti-glug, assicurano un versamento più rapido e un minor spreco di olio.Inoltre, PLI ha anche introdotto una nuova confezione Bag-in-a-Box che utilizza il 92% di plastica in meno rispetto alla versione originale, riducendo drasticamente rifiuti e inquinamento. |